A Direct Acting Solenoid Valve is a crucial component in many fluid control systems, widely used in various industrial and commercial applications. This valve operates using the direct force of an electromagnet to control the flow of fluids such as air, water, oil, or gas. Unlike other solenoid valves that rely on auxiliary pressure, a Direct Acting Solenoid Valve directly actuates the valve’s mechanism by the electromagnetic force created when an electric current passes through the solenoid coil. In this article, we will explore how Direct Acting Solenoid Valves work, their key features, and their diverse applications.
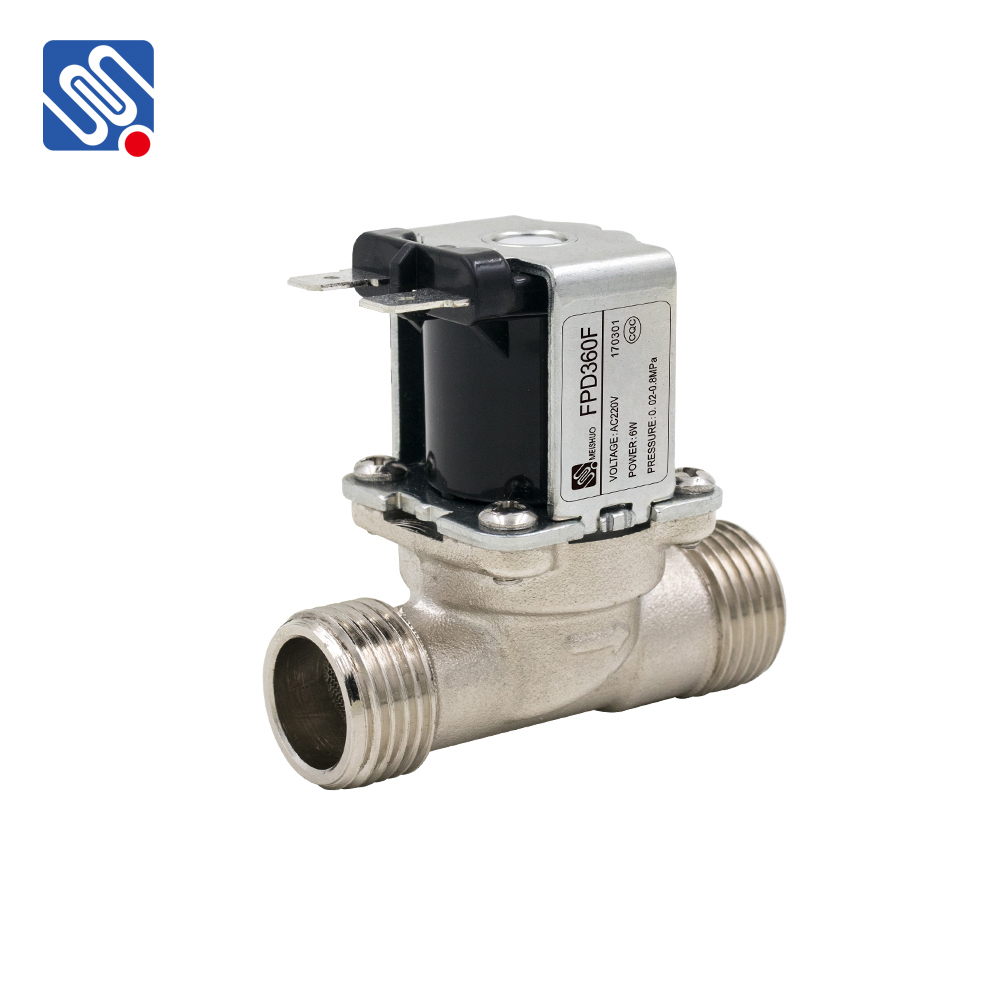
How Direct Acting Solenoid Valves Work The core of the Direct Acting Solenoid Valve is the solenoid coil, a tightly wound wire that becomes magnetized when electric current is passed through it. The magnetic field generated by the coil exerts a force on a plunger or armature, which is typically located within the valve. This force either opens or closes the valve, allowing or blocking the passage of the fluid. In its default state, the valve may be normally open (NO) or normally closed (NC). When the solenoid coil is energized, the magnetic field pulls the plunger to a new position, altering the valve’s state. For example, in a normally closed valve, energizing the coil pulls the plunger away from the valve seat, opening the valve and allowing fluid to pass through. When the coil is de-energized, the plunger returns to its initial position, closing the valve and stopping the flow.
Leave a Reply